Schaumstoff
Schaumstoffesind künstlich hergestellte Stoffe mitzellförmiger (oderzelliger) Struktur.Die einzelnen Zellen sind hohl und i. d. R. mit Luft gefüllt, so dass Schaumstoffe leicht sind. Sie haben eine niedrigeDichte.Für ihre Herstellung (Schäumen) eignen sich fast alleKunststoffe.Schaumstoffe kann man zusammendrücken, also durch Druck ihr Volumen deutlich verkleinern (sieheKompressibilität).
Schaumstoffe ausnatürlichemundsynthetischemKautschuk (Porengummi,Zellkautschuk) zählen zu den ältesten und werden alsSchaumgummibezeichnet. Außerdem gibt es Schaumstoffe aus Mineral (Perlit,Porenbeton,Schwämme,Knochen), Zellstoff (Kork), Protein (Soufflé) sowieMetallschäume.
Einteilung
[Bearbeiten|Quelltext bearbeiten]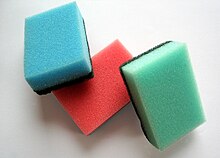
- Geschlossenzelliger Schaumstoff – die Wände zwischen den einzelnen Zellen sind komplett geschlossen. Feste und halbfeste Schaumstoffe sind meist geschlossenzellig und können andereTreibgaseals Luft enthalten, etwaCO2.
- Offenzelliger Schaumstoff – die Zellwände sind nicht geschlossen, diese Schaumstoffe sind meist weich, enthalten Luft und könnenFlüssigkeitenaufnehmen. Sie eignen sich zurSchalldämmungluftübertragenen Schalls.
- Gemischtzellige Schaumstoffe enthalten beide Arten von Zellen. Zum BeispielStyropor:geschlossenzellige Kügelchen verpresst zu grösseren offenzelligen (porösen) Gebilden.
- Integralschäume haben eine geschlossene dicke Außenhaut und einen zelligen Kern, dieDichtenimmt nach innen hin ab.
Eigenschaften
[Bearbeiten|Quelltext bearbeiten]

Schaumstoffe bestehen überwiegend aus Luft und haben eine geringe Dichte (hierRaumgewichtgenannt) undWärmeleitfähigkeitbei eher geringerFestigkeit.Die Zellen der meisten Schaumstoffe sind zwischen 0,05 und 1 mm groß.
- DieStauchhärteoderEindruckhärtegibt jenenDruckan, bei der sich der Schaumstoff um 10 % verformt. Schaumstoffe mit Stauchhärten von mehr als 80 kPa sind fest, jene zwischen 15 und 80 kPa halbfest, jene mit weniger als 15 kPa weich.
- DasRaumgewichtwird in kg/m³ angegeben.
Die Stauchhärte hängt vomRaumgewichtdes Schaumstoffs und vomElastizitätsmoduldes verwendeten Kunststoffs ab. Im Allgemeinen gilt: je dichter, desto fester.[1]
Bei Schaumstoffen ist der Anteil des Kunststoff-Zellengerüsts (abhängig vom Raumgewicht) meist weit geringer als der Anteil des füllenden Gases. Beispielsweise besteht ein Schaumstoff mit einem Raumgewicht von 10 kg/m³ zu 99 % aus Luft (oder einem anderen Treibgas).
DiewärmedämmendeWirkung hängt vor allem von derWärmeleitfähigkeitdes füllenden Gases ab, wobei mitFCKWgefüllte Schaumstoffe besser isolieren als luftgefüllte. Offenzellige Schaumstoffe können Wasser aufnehmen, was ihre Wärmeleitfähigkeit erhöht.
Schäumverfahren
[Bearbeiten|Quelltext bearbeiten]Unterscheidung nach der Herstellungsart:
- Physikalisches Schäumen: Das Material wird durch einen physikalischen Vorgang geschäumt.
- Chemisches Schäumen: DemKunststoffgranulatwird ein Treibmittel, meist in Form eines so genannten Masterbatchgranulates, zugegeben. Durch Wärmezufuhr spaltet sich ein flüchtiger Bestandteil des Treibmittels ab, was zum Aufschäumen der Schmelze führt.
- Mechanisches Schäumen: Hierbei wird Luft in das zu schäumende Harz oder die Paste eingerührt; durch Vernetzen des Harzes oder durch Gelieren der Paste verfestigt sich dieser Schaumstoff.
Schaumextrusion
[Bearbeiten|Quelltext bearbeiten]Bei der Herstellung vonPP-E-Schaum (ebenso möglich ist dies fürPolyethylen,Polystyrol,PEToder einigeBiopolymere) wird aufgeschmolzenesPolypropylenimExtruderunter hohen Drücken mit Treibgas (z. B.Pentan,CO2) versetzt. Früher wurden als Treibmittel oftFCKWeingesetzt, deren Verwendung aber aufgrund der schädigenden Wirkung auf dieOzonschichtinzwischen weitestgehend verboten ist.
Beim Austreten aus einer Lochdüse expandiert der Kunststoff auf das 20- bis 50-fache Volumen. Die entstehenden Schaumstränge können zum einen durch rotierende Messer imWasserringgranulatoroderUnterwassergranulatorzu Schaumpartikeln von ca. 2–8 mm Durchmesser gekürzt werden. Sie werden dann vom Wasser abgeschieden, getrocknet, in Silos konditioniert und dann im sog. Formteilprozess zu Schaumformteilen verarbeitet.
Ein sehr wichtiger Prozess ist die Herstellung geschäumter Folien (z. B. aus PP oder PE alsTrittschalldämmung) oder geschäumter Platten (z. B. XPS aus Polystyrol). Das kontinuierlicheExtrusionsverfahrenwird dabei aber in den meisten Fällen mit so genannten Kaskadenextrudern, also zwei hintereinander angeordneten Extrudern, durchgeführt. Während im ersten Extruder, wie schon erwähnt, das Kunststoffgranulat aufgeschmolzen („plastifiziert “) wird, wird nach Zugabe des Treibmittels im zweiten Extruder dieses Treibmittel sehr gleichmäßig eingemischt. Zudem wird dabei die Schmelze auf ein definiertes Temperaturniveau gebracht (meistens ein Abkühlprozess), wonach diese dann in einem Breitschlitzwerkzeug auf die ungefähre Breite der späteren Folie oder Platte gebracht wird. Durch den im Verhältnis zumDampfdruckdes Treibmittels geringeren Umgebungsdruck expandiert die Schmelze und wird in einer speziellen Vorrichtung auf die gewünschte Plattendicke kalibriert. Die nachfolgenden Aggregate schneiden die Platten auf das gewünschte Maß bzw. wickeln die Folie auf, so dass die Produkte dann für eine Weiterverarbeitung zur Verfügung stehen.
Formteilprozess
[Bearbeiten|Quelltext bearbeiten]Der Formteilprozess dient zur Verarbeitung von Schaumstoffpartikeln (EPS,EPP,EPE) zu Schaumstoffformteilen.
Schaumstoffkügelchen mit Durchmessern von ca. 1–8 mm werden in poröse Aluminiumformen eingeblasen und mittelsWasserdampf(ca. 1,2 bar für EPS, ca. 3 bar bei EPP) miteinander versintert. Nach der Abkühl- und Stabilisierphase können die neu entstandenen Formteile entformt werden.
Dieses Herstellverfahren ermöglicht es,thermoplastischeSchaumteile imDichtebereichzwischen ca. 12 kg/m³ und 300 kg/m³ bei sehr homogener Dichteverteilung über das gesamte Schaumteil herzustellen. Direktschäumverfahren mit chemischen oder physikalischen Treibgasen beimSpritzgusserlauben dies wegen der begrenzten Abkühlgeschwindigkeit bei größeren Wandstärken nicht.
Der Formteilprozess ist sehrenergieintensiv,da bei jedem Zyklus (Schuss) das Werkzeug (Form) und Teile desFormteilautomaten(Dampfkammer) aufgeheizt und wieder abgekühlt werden müssen.
Anwendungsgebiete der EPP-Formteile sind z. B. Isolierbehälter, Heizungsisolationen, Mehrwegtransportverpackungen und in zunehmendem Maße Automobilteile wie Stoßfängerkerne, Sonnenblenden, Crashpads, Toolboxen (die in der Ersatzradfelge liegen und z. B. Anhängerkupplung, Wagenheber und Bordwerkzeug aufnehmen) oder Freizeitartikel.[2]
Die Schaumextrusion von Partikelschaumstoffen bietet folgende Vorteile gegenüber imAutoklavenhergestellten Partikelschäumen:
- Kostengünstige Herstellung, da ein Verfahrensschritt entfällt (Autoklavbehandlung)
- Einfacherer und schnellerer Farbwechsel
Nachteile des Extrusionsmaterials hingegen sind eine durchschnittlich höhere Verarbeitungstemperatur, verbunden mit einem höheren Energieverbrauch und teilweise deutlich schlechtere mechanische Eigenschaften relativ zur Dichte im Vergleich zu Autoklavmaterial.
Styroporverfahren
[Bearbeiten|Quelltext bearbeiten]Expandiertes Polystyrol (EPS) wird durch physikalisches Schäumen hergestellt: Das treibmittelhaltigeGranulat(5 %Pentan) wird zunächst durch Erhitzen mitWasserdampfbei ca. 105 °C bis auf das 40 bis 80-fache Volumen vorgeschäumt und danach zwischen 3 und 48 Stunden bei Raumtemperatur zwischengelagert, so dass danach das Pentan bis auf einen Anteil von ca. 3 % entweichen und Luft eindringen kann. Somit wird die Entstehung eines Vakuums im Inneren vermieden. Beim Fertigschäumen wird das vorgeschäumte EPS in eine Form gefüllt und durch weiteres Erhitzen auf ca. 130 °C mit Wasserdampf expandiert, das heißt, es füllt die Form und die einzelnen Teilchen verschmelzen an den Rändern. Bei großen Blockformen wird meist zudem vor dem Einbringen des Wasserdampfes ein Vakuum angelegt, um das Expandieren der EPS-Teilchen zu begünstigen.
Die Dichte wird durch den Vorschäumgrad bestimmt. Wird dieser jedoch zu groß, so fällt das fertige Produkt zusammen.
Thermoplast-Schaumguss-Verfahren (TSG)
[Bearbeiten|Quelltext bearbeiten]Durch Zugabe von Treibmitteln zu einer Reihe vonThermoplasten,auch solche mitFüllstoffen(Glas-oderKarbonfasern) lassen sich Schaumstrukturen in Spritzgussteilen erstellen. Die Treibmittel können je nach Art und Konsistenz dem Granulat in wenigen Prozent zugemischt oder der Schmelze im Zylinder in flüssigem Zustand unter hohem Druck zugepumpt werden. Im Kern besitzen die entstehenden Formteile eine Schaumstruktur, zur Oberfläche hin eine weitgehend kompakte Außenhaut. Das Verfahren wird angewendet, um z. B. dickwandige Partien an Spritzgussteilen mit einem Schaumkern zu versehen, um Einfallstellen zu vermeiden bis hin zur Innenschäumung relativ dickwandiger Formteile, um Gewicht sparen zu können, ohne die Wanddicke reduzieren zu müssen. Man wendet das Verfahren bei Wanddicken ab 2 mm, aber meist bei Wanddicken zwischen 4 und 20 mm an.
Die erforderlichen Drücke für den Einspritzvorgang in das Werkzeug und den Nachdruck sind erheblich niedriger als für das normale Spritzgießen. So sind die Maschinen meist nur mit Einspritzdrücken bis ca. 1000 bar ausgestattet. Die großen Schussgewichte realisiert man oft mit Kolbeneinspritzaggregaten, die durch eine Vorplastifizierschnecke befüllt werden. Ein Nachdruck kann meist entfallen, da die Konturbildung in der Werkzeughöhlung durch die Expansion des Treibmittels erfolgt. Abgesehen von dem zuletzt genannten Unterschied ist das Verfahren dem normalen Spritzgießen prinzipiell sehr ähnlich. Jede normale Spritzgießmaschine ist für das Verfahren verwendbar.
Das TSG-Verfahren eignet sich dafür, besonders steife Konstruktionen zu erstellen, da beliebige Wanddickenunterschiede herstellbar sind, ohne dass Einfallstellen entstehen. Häufig werden auf Rundtischmaschinen mehrere Werkzeuge nacheinander eingespritzt. Damit wird die Ausbringung trotz langer Kühlzeiten (durch die großen Wanddicken) verbessert.
PUR-Schäumen
[Bearbeiten|Quelltext bearbeiten]Hier werden im Gegensatz zum Styroporverfahren flüssige, reaktionsfähige Ausgangsstoffe vom Verarbeiter verwendet. Werden Polyole mit Isocyanaten und dem Treibmittel (meist Wasser) vermischt, so reagiert das Polyol mit dem Isocyanat in einer Polyaddition zu PUR (Polyurethanschaum) und das Treibmittel bildet Gaseinschlüsse (bei dem Treibmittel Wasser reagiert dieses mit einem Teil des Isocyanates, wobei Kohlendioxid freigesetzt wird). Zusatzstoffe wie auch das Treibmittel werden im Polyol beigemengt, so dass meist zwei Komponenten zum Einsatz kommen.
Je nach Auswahl der Ausgangsstoffe können die Eigenschaften eingestellt werden. So erhält man bei Verwendung von langkettigen Polyolen weiche bis elastische Schäume, oder bei kurzkettigen Polyolen stark vernetzte harte Schaumstoffe.
Als Hauptverfahren kann man das kontinuierliche Bandschäumen und die beiden diskontinuierlichen RSG (Reaktionsschaumguss) undRIM(Reaktion-Injektions-Moulding) bzw. Niederdruck und Hochdruck-Verfahren, wobei das Letztere immer mehr Verbreitung findet, nennen.
Bei den diskontinuierlichen Verfahren muss beachtet werden, dass Ringleitungen installiert werden, um ein „Abstehen “oder ein Entmischen zu verhindern, denn z. B. das Isocyanat sollte über 15 °C warm sein, da es sonst kristallisiert. Des Weiteren sollte auch ein Reinigungssystem für den Mischkopf vorgesehen werden, um ein Verkleben zu verhindern.
Beim RRIM (Reinforced Reaction Injection Moulding) werden zwei Komponenten (PolyolundIsocyanat) und ein Verstärkungsstoff (z. B.Glasfaser,Kohlenstofffaser,Gesteinsmehl) im so genannten Mischkopf gemischt und unter hohem Druck in ein formgebendes Werkzeug gespritzt. Nach derexothermenReaktion der Komponenten ist derduroplastischeKunststoffPolyurethanentstanden und kann dem Werkzeug entnommen werden. Anwendungsbeispiele sind Außenhautteile in der Automobilindustrie, wie Kotflügel, Schweller- und Stoßfängerverkleidungen. Ein Vorteil des Polyurethans gegenüber thermoplastischen Kunststoffen liegt in der relativ hohen Wärmeformbeständigkeit.
MuCell-Verfahren
[Bearbeiten|Quelltext bearbeiten]Im MuCell-Verfahren wird der thermoplastischen Kunststoffschmelze eininertes Gas(entweder Stickstoff oder Kohlendioxid) zugeführt und im Schmelzezylinder zu einer Einphasenlösung gemischt. Beim Einspritzen dieser Einphasenlösung in die Kavität des Spritzgieß- oder Blasformwerkzeugs, bzw. bei der Extrusion bei Austritt aus der Düse, erfährt das Gemisch einen Druckabfall, was dazu führt, dass das Gas über das Bauteil verteilt nukleiert und Millionen von kleinsten Zellen wachsen. Diese Zellen ersetzen dann ein definiertes Volumen, was zu einer Dichtereduzierung im Bauteil führt.
Neuere Entwicklungen
[Bearbeiten|Quelltext bearbeiten]Bei herkömmlichen Herstellungsprozessen werden Schäume häufig aus Polymerschmelzen und gasförmigen Treibmitteln gewonnen. Eine Alternative besteht darin, mikroskopisch kleine Schablonen (sogenannteTemplates) zu benutzen, um dem Schaum die richtige Struktur zu verleihen. Beispielsweise können winzige Wassertröpfchen in einer Monomerlösung feinst verteilt und nach der Polymerisation entfernt werden. Ein anderes Verfahren nutzt Partikel, um Luftblasen in der Reaktionsmischung zu stabilisieren. Ein neu entwickeltes Verfahren zur Herstellung vonexpandiertem Polystyrolbasiert auf der Polymerisation geschäumter Öl-in-Wasser-Emulsionen.Styrol(Ölphase) wird zunächst in einer wässerigen Phase emulgiert. Dann wird die durch ein anionischesTensidstabilisierte Emulsion mit Stickstoff aufgeschäumt. Dabei entstehen Schaumblasen, die von dicht gepackten Emulsionstropfen umgeben sind. Im abschließenden Schritt wird die Polymerisation durch Bestrahlung mit UV-Licht ausgelöst. Die Emulsionstropfen reagieren dabei, wobei die Struktur des Schaums erhalten bleibt. Die entstandenen Polymerschäume enthalten Poren, die teilweise miteinander verbunden sind. Hierdurch wird der Durchfluss von Luft,Fluidenoder anderen Materialien durch den Schaum ermöglicht, was die Anwendung für beispielsweise Filtermaterialien oder bioinspirierte Gerüststrukturen interessant macht.[3]
Beispiele
[Bearbeiten|Quelltext bearbeiten]- Thermoplastische Schäume (z. B.PS-E,PP-EundPVC-E)
- ElastomereSchäume (z. B.PUR-Weichschaum,NBR)
- Duroplastische Schäume (z. B. PUR-Hartschaum,PF)
Siehe auch
[Bearbeiten|Quelltext bearbeiten]Weblinks
[Bearbeiten|Quelltext bearbeiten]Einzelnachweise
[Bearbeiten|Quelltext bearbeiten]- ↑Ullmann's Encyclopedia of Industrial Chemistry.7. Auflage. 2005, Foamed Plastics,doi:10.1002/14356007.a11_435.
- ↑EPP-Forum in Bayreuth:Expandiertes Polypropylen Netzwerk für EPP
- ↑Fabian Schüler, Debora Schamel, Anniina Salonen,Wiebke Drenckhan,Michael D. Gilchrist, Cosima Stubenrauch:Synthese von makroporösem Polystyrol durch Polymerisation geschäumter Emulsionen.In:Angewandte Chemie.Band124,Nr.9,2012,ISSN1433-7851,S.2256–2260,doi:10.1002/ange.201107806.