Rayon
Rayon,also calledviscose[1]and commercialised in some countries assabra silkorcactus silk,[2]is asemi-synthetic fiber,[3]made from natural sources of regeneratedcellulose,such as wood and related agricultural products.[4]It has the same molecular structure as cellulose. Many types and grades of viscose fibers and films exist. Some imitate the feel and texture ofnatural fiberssuch assilk,wool,cotton,andlinen.The types that resemble silk are often calledartificial silk.It can be woven or knit to make textiles for clothing and other purposes.[5]
Rayon production involvessolubilizingcellulose to allow turning the fibers into required form. Three common solubilization methods are:
- Thecuprammoniumprocess (not in use today), usingammoniacalsolutions of copper salts[6]
- The viscose process, the most common today,[7][8]usingalkaliandcarbon disulfide
- TheLyocellprocess, usingamine oxide,which avoids producing neurotoxic carbon disulfide but is more expensive[9][10]
History[edit]
French scientist and industrialistHilaire de Chardonnet(1838–1924) invented the first artificial textile fiber,artificial silk.[11]
SwisschemistMatthias Eduard Schweizer(1818–1860) discovered that cellulose dissolved intetraaminecopper dihydroxide.Max FremeryandJohann Urbandeveloped a method to producecarbon fibersfor use inlight bulbsin 1897.[12]Production ofcuprammonium rayonfortextilesstarted in 1899 in theVereinigte Glanzstoff Fabriken AGinOberbruch(nearAachen).[citation needed][13]Improvement byJ. P. Bemberg AGin 1904 made the artificial silk a product comparable to real silk.[14][15]
English chemistCharles Frederick Crossand his collaborators,Edward John Bevanand Clayton Beadle, patented their artificial silk in 1894. They named it "viscose" because its production involved the intermediacy of a highly viscous solution. Cross and Bevan took out British Patent No. 8,700, "Improvements in Dissolving Cellulose and Allied Compounds" in May, 1892.[16]In 1893, they formed the Viscose Syndicate to grant licences and, in 1896, formed the British Viscoid Co. Ltd.[11][17]
The first commercial viscose rayon was produced by the UK companyCourtaulds Fibresin November 1905.[18]In the UK, rayon production enjoyed tariff protection earlier than most other industries.[19][20]Courtaulds formed an American division,American Viscose(later known as Avtex Fibers), to produce their formulation in the US in 1910.[21]The name "rayon" was adopted in 1924[citation needed],with "viscose" being used for the viscous organic liquid used to make both rayon andcellophane.In Europe, though, the fabric itself became known as "viscose", which has been ruled an acceptable alternative term for rayon by the USFederal Trade Commission(FTC).[citation needed]
Rayon was produced only as a filament fiber until the 1930s, when methods were developed to utilize "broken waste rayon" asstaplefiber.[citation needed]
Manufacturers' search for a less environmentally-harmful process for making Rayon led to the development of the lyocell method for producing Rayon.[22]The lyocell process was developed in 1972 by a team at the now defunctAmerican Enkafibers facility atEnka, North Carolina.[citation needed]In 2003, theAmerican Association of Textile Chemists and Colorists(AATCC) awarded Neal E. Franks their Henry E. Millson Award for Invention for lyocell.[23]In 1966–1968, D. L. Johnson of Eastman Kodak Inc. studied NMMO solutions. In the decade 1969 to 1979,American Enkatried unsuccessfully to commercialize the process.[22]The operating name for the fibre inside the Enka organization was "Newcell", and the development was carried through pilot plant scale before the work was stopped. The basic process of dissolving cellulose inNMMOwas first described in a 1981 patent by Mcorsley for Akzona Incorporated[22][24](the holding company of Akzo). In the 1980s the patent was licensed byAkzoto Courtaulds and Lenzing.[25]The fibre was developed byCourtauldsFibres under the brand name "Tencel" in the 1980s. In 1982, a 100 kg/week pilot plant was built in Coventry, UK, and production was increased tenfold (to a ton/week) in 1984. In 1988, a 25 ton/week semi-commercial production line opened at theGrimsby, UK, pilot plant.[26][22]The process was first[citation needed]commercialized at Courtaulds' rayon factories atMobile, Alabama[27](1990[citation needed]), and at the Grimsby plant (1998)[citation needed].In January 1993, the Mobile Tencel plant reached full production levels of 20,000 tons per year, by which time Courtaulds had spent £100 million and 10 years on Tencel development. Tencel revenues for 1993 were estimated as likely to be £50 million. A second plant in Mobile was planned.[27]By 2004, production had quadrupled to 80,000 tons.[25]
Lenzing began a pilot plant in 1990,[22]and commercial production in 1997, with 12 metric tonnes/year made in a plant inHeiligenkreuz im Lafnitztal,Austria.[22][25]When an explosion hit the plant in 2003 it was producing 20,000 tonnes/year, and planning to double capacity by the end of the year.[28]In 2004 Lenzing was producing 40,000tons[sic, probably metric tonnes].[25]In 1998, Lenzing and Courtaulds reached a patent dispute settlement.[25]
In 1998 Courtaulds was acquired by competitorAkzo Nobel,[29]which combined the Tencel division with other fibre divisions under the Accordis banner, then sold them to private equity firmCVC Partners.In 2000, CVC sold the Tencel division toLenzing AG,which combined it with their "Lenzing Lyocell" business, but maintained the brand name Tencel.[25]It took over the plants in Mobile and Grimsby, and by 2015 were the largest lyocell producer at 130,000 tonnes/year.[22]
Process[edit]
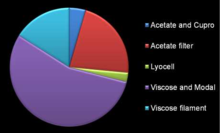
Rayon is produced by dissolving cellulose, then converting this solution back to insoluble fibrous cellulose. Various processes have been developed for this regeneration. The most common methods for creating rayon are thecuprammoniummethod, the viscose method, and the lyocell process. The first two methods have been practiced for more than a century.
Cuprammonium methods[edit]
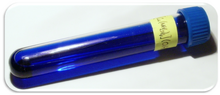
Cuprammonium rayon has properties similar to viscose; however, during its production, the cellulose is combined withcopperandammonia(Schweizer's reagent). Due to the detrimental environmental effects of this production method, cuprammonium rayon is no longer being produced in theUnited States.[30]The process has been described as obsolete,[6]but cuprammonium rayon is still made by one company in Japan.[31][better source needed]
Tetraamminecopper(II) sulfateis also used as a solvent.
Viscose method[edit]

The viscose process builds on the reaction ofcellulosewith a strong base, followed by treatment of that solution withcarbon disulfideto give axanthatederivative. The xanthate is then converted back to a cellulose fiber in a subsequent step.
The viscose method can usewoodas a source of cellulose, whereas other routes to rayon requirelignin-free cellulose as a starting material. The use of woody sources of cellulose makes viscose cheaper, so it was traditionally used on a larger scale than the other methods. On the other hand, the original viscose process generates large amounts of contaminated wastewater. Newer technologies use less water and have improved the quality of the wastewater.
The raw material for viscose is primarilywood pulp(sometimesbamboo pulp), which is chemically converted into a soluble compound. It is then dissolved and forced through aspinneretto produce filaments, which are chemically solidified, resulting in fibers of nearly pure cellulose.[32]Unless the chemicals are handled carefully, workers can be seriously harmed by thecarbon disulfideused to manufacture most rayon.[33][34]
To prepare viscose, pulp is treated with aqueous sodium hydroxide (typically 16–19%by mass) to form "alkali cellulose",which has the approximate formula [C6H9O4−ONa]n.This material is allowed to depolymerize to an extent. The rate of depolymerization (ripening or maturing) depends on temperature and is affected by the presence of various inorganic additives, such as metal oxides and hydroxides. Air also affects the ripening process, since oxygen causes depolymerization. The alkali cellulose is then treated with carbon disulfide to form sodium cellulosexanthate:[5]
Rayon fiber is produced from the ripened solutions by treatment with a mineral acid, such assulfuric acid.In this step, the xanthate groups are hydrolyzed to regenerate cellulose and carbon disulfide:
Aside from regenerated cellulose, acidification giveshydrogen sulfide(H2S), sulfur, and carbon disulfide. The thread made from the regenerated cellulose is washed to remove residual acid. The sulfur is then removed by the addition ofsodium sulfidesolution, and impurities are oxidized by bleaching withsodium hypochloritesolution orhydrogen peroxidesolution.[17]
Production begins with processed cellulose obtained from wood pulp and plant fibers. The cellulose content in the pulp should be around 87–97%.
The steps:[32]
- Immersion: The cellulose is treated withcaustic soda.
- Pressing. The treated cellulose is then pressed between rollers to remove excess liquid.
- The pressed sheets are crumbled or shredded to produce what is known as "white crumb".
- The "white crumb" is aged through exposure tooxygen.This is a depolymerization step and is avoided in the case of polynosics.
- The aged "white crumb" is mixed in vats with carbon disulfide to form the xanthate. This step produces "orange-yellow crumb".
- The "yellow crumb" is dissolved in a caustic solution to form viscose. The viscose is set to stand for a period of time, allowing it to "ripen". During this stage the molecular weight of the polymer changes.
- After ripening, the viscose is filtered, degassed, and then extruded through aspinneretinto a bath ofsulfuric acid,resulting in the formation of rayon filaments. The acid is used as a regenerating agent. It converts cellulose xanthate back to cellulose. The regeneration step is rapid, which does not allow proper orientation of cellulose molecules. So to delay the process of regeneration,zinc sulfateis used in the bath, which converts cellulose xanthate to zinc cellulose xanthate, thus providing time for proper orientation to take place before regeneration.
- Spinning.The spinning of viscose rayon fiber is done using a wet-spinning process. The filaments are allowed to pass through a coagulation bath after extrusion from the spinneret holes. The two-way mass transfer takes place.
- Drawing.The rayon filaments are stretched, in a procedure known as drawing, to straighten out the fibers.
- Washing.The fibers are then washed to remove any residual chemicals from them.
- Cutting.If filament fibers are desired, then the process ends here. The filaments are cut down when producing staple fibers.
Lyocell method[edit]

Thelyocellprocess relies on dissolution of cellulose products in a solvent,N-methyl morpholine N-oxide(NMMO).
The process starts with cellulose and involves dry jet-wet spinning. It was developed at the now defunctAmerican Enka CompanyandCourtauldsFibres. Lenzing's Tencel is an example of a lyocell fiber.[14]Unlike the viscose process, the lycocell process does not use highly toxic carbon sulfide.[9][10]"Lyocell" has become a genericized trademark, used to refer to the lyocell process for making cellulose fibers.[10]
As of 2018[update],the lyocell process is not widely used, because it is still more expensive than the viscose process.[10][9]
Properties[edit]



Rayon is a versatile fiber and is widely claimed to have the same comfort properties as natural fibers, although thedrapeand slipperiness of rayon textiles are often more likenylon.It can imitate the feel and texture ofsilk,wool,cottonandlinen.The fibers are easilydyedin a wide range of colors. Rayon fabrics are soft, smooth, cool, comfortable, and highly absorbent, but they do not always insulate body heat, making them ideal for use in hot and humid climates, although also making their "hand" (feel) cool and sometimes almost slimy to the touch.[35]
The durability and appearance retention of regular viscose rayons are low, especially when wet; also, rayon has the lowest elastic recovery of any fiber. However, HWM rayon (high-wet-modulus rayon) is much stronger and exhibits higher durability and appearance retention. Recommended care for regular viscose rayon is dry-cleaning only. HWM rayon can be machine-washed.[36]
Regular rayon has lengthwise lines calledstriationsand its cross-section is an indented circular shape. The cross-sections of HWM and cupra rayon are rounder.Filamentrayonyarnsvary from 80 to 980 filaments per yarn and vary in size from 40 to 5000denier.Staple fibersrange from 1.5 to 15 denier and are mechanically or chemically crimped. Rayon fibers are naturally very bright, but the addition of delusteringpigmentscuts down on this natural brightness.[36]
Structural modification[edit]
The physical properties of rayon remained unchanged until the development of high-tenacity rayon in the 1940s. Further research and development led to high-wet-modulus rayon (HWM rayon) in the 1950s.[36]Research in the UK was centred on the government-fundedBritish Rayon Research Association.
High-tenacity rayonis another modified version of viscose that has almost twice the strength of HWM. This type of rayon is typically used for industrial purposes such as tire cord.[30]
Industrial applications of rayon emerged around 1935. Substituting cotton fiber in tires and belts, industrial types of rayon developed a totally different set of properties, amongst which tensile strength and elastic modulus were paramount.
Modalis agenericized trademarkofLenzing AG,used for (viscose) rayon which is stretched as it is made, aligning the molecules along the fibers. Two forms are available: "polynosics" and "high wet modulus" (HWM).[37][38][better source needed]High-wet-modulus rayonis a modified version of viscose that is stronger when wet. It can bemercerizedlike cotton. HWM rayons are also known as "polynosic".[contradictory]Polynosic fibers are dimensionally stable and do not shrink or get pulled out of shape when wet like many rayons. They are also wear-resistant and strong while maintaining a soft, silky feel. They are sometimes identified by the trade name Modal.[30]Modal is used alone or with other fibers (often cotton orspandex) in clothing and household items like pajamas, underwear, bathrobes, towels, and bedsheets. Modal can betumble-driedwithout damage.[39]The fabric has been known topillless than cotton due to fiber properties and lower surface friction.[38]The trademarked Modal is made by spinning beech-tree cellulose and is considered a more eco-friendly alternative to cotton, as the production process uses on average 10–20 times less water.[40]
Producers and brand names[edit]
In 2018, viscose fiber production in the world was approximately 5.8 million tons, andChinawas the largest producer with about 65% of total global production.[41]Trade namesare used within the rayon industry to label the type of rayon in the product. Viscose rayon was first produced in Coventry, England in 1905 by Courtaulds.
Bembergis a trade name forcupramonium rayondeveloped byJ. P. Bemberg.Bemberg performs much like viscose but has a smaller diameter and comes closest to silk in feel. Bemberg is now only produced in Japan.[31]The fibers are finer than viscose rayon.[15][failed verification]
ModalandTencelare widely used forms of rayon produced byLenzing AG.Tencel, generic namelyocell,is made by a slightly different solvent recovery process, and is considered a different fiber by the US FTC. Tencel lyocell was first produced commercially byCourtaulds' Grimsby plantin England. The process, which dissolves cellulose without a chemical reaction, was developed by Courtaulds Research.
Birla Celluloseis also a volume manufacturer of rayon. They have plants located inIndia,IndonesiaandChina.
Accordiswas a major manufacturer of cellulose-based fibers and yarns. Production facilities can be found throughout Europe, the U.S. andBrazil.[42]
Visil rayonand HOPE FR areflame retardantforms of viscose that havesilicaembedded in the fiber during manufacturing.
North American Rayon CorporationofTennesseeproduced viscose rayon until its closure in the year 2000.[43][44]
Indonesiais one of the largest producers of rayon in the world, andAsia Pacific Rayon(APR) of the country has an annual production capacity of 0.24 million tons.[45]
Environmental impact[edit]
Thebiodegradabilityof various fibers in soil burial and sewage sludge was evaluated by Korean researchers. Rayon was found to be more biodegradable than cotton, and cotton more than acetate. The more water-repellent the rayon-based fabric, the more slowly it will decompose.[46]Silverfish—like thefirebrat—can eat rayon, but damage was found to be minor, potentially due to the heavy, slick texture of the tested rayon.[47]Another study states that "artificial silk [...] [was] readily eaten" by thegrey silverfish.[48]
A 2014 ocean survey found that rayon contributed to 56.9% of the total fibers found indeep oceanareas, the rest beingpolyester,polyamides,acetateandacrylic.[49]A 2016 study found a discrepancy in the ability to identify natural fibers in a marine environment viaFourier transform infrared spectroscopy.[50]Later research of oceanic microfibers instead found cotton being the most frequent match (50% of all fibers), followed by other cellulosic fibers at 29.5% (e.g., rayon/viscose, linen, jute, kenaf, hemp, etc.).[51]Further analysis of the specific contribution of rayon to ocean fibers was not performed due to the difficulty in distinguishing between natural and man-made cellulosic fibers using FTIR spectra.
For several years, there have been concerns about links between rayon manufacturers and deforestation. As a result of these concerns,FSCandPEFCcame on the same platform with CanopyPlanet to focus on these issues. CanopyPlanet subsequently started publishing a yearly Hot Button report, which puts all the man-made cellulosics manufacturers globally on the same scoring platform. The scoring from the 2020 report scores all such manufacturers on a scale of 35, the highest scores having been achieved byBirla Cellulose(33) andLenzing(30.5).
Carbon disulfide toxicity[edit]
Carbon disulfide ishighly toxic.[52]It is well documented to have seriously harmed the health of rayon workers in developed countries, and emissions may also harm the health of people living near rayon plants[52]and their livestock.[53]Rates of disability in modern factories (mainly in China, Indonesia, and India) are unknown.[34][7]This has raised ethical concerns over viscose rayon production.[8][7][9][33]As of 2016[update],production facilities located in developing countries generally do not provide environmental or worker safety data.[54]
Most global carbon disulfide emissions come from rayon production, as of 2008.[55]As of 2004[update],about 250 g of carbon disulfide is emitted per kilogram of rayon produced.[56]
Control technologies have enabled improved collection of carbon disulfide and reuse of it, resulting in a lower emissions of carbon disulfide.[5]These have not always been implemented in places where it was not legally required and profitable.[53]
Carbon disulfide isvolatileand is lost before the rayon gets to the consumer; the rayon itself is basically purecellulose.[33]
Studies from the 1930s show that 30% of American rayon workers experienced significant health impacts due tocarbon disulfideexposure.Courtauldsworked hard to prevent this information being published in Britain.[8]
During theSecond World War,political prisoners inNazi Germanywere made to work in appalling conditions at the Phrix rayon factory inKrefeld.[57]Nazis usedforced labourto produce rayon across occupied Europe.[8]
In the 1990s, viscose rayon producers faced lawsuits for negligentenvironmental pollution.Emissions abatement technologieshad been consistently used.Carbon-bed recovery,for instance, which reduces emissions by about 90%, was used in Europe, but not in the US, by Courtaulds.[53]Pollution controland worker safety started to becomecost-limiting factorsin production.
Japan has reduced carbon disulfide emissions per kilogram of viscose rayon produced (by about 16% per year), but in other rayon-producing countries, including China, emissions are uncontrolled. Rayon production is steady or decreasing except in China, where it is increasing, as of 2004[update].[56]
Rayon production has largely moved to the developing world, especially China, Indonesia and India.[7][8]Rates of disability in these factories are unknown, as of 2016[update],[34][7]and concerns for worker safety continue.[54]
Controversy[edit]
Studies have found the production of rayon can be potentially detrimental to the health of factory workers.[58][59]Workers in the factories that are exposed to these chemicals are at high risk of hysteria, stroke and nerve damage and when those chemicals are disposed into the water not only does it affect the eco-system, but the whole community can be poisoned.[60]
Related materials[edit]
Related materials are not regenerated cellulose, butestersof cellulose.[61][62]
Nitrocelluloseis a derivative of cellulose that is soluble in organic solvents. It is mainly used as an explosive or as alacquer.Many early plastics, includingcelluloid,were made from nitrocellulose.
Celluloseacetateshares many traits with viscose rayon and was formerly considered the same textile. However, rayon resists heat, while acetate is prone to melting. Acetate must be laundered with care either by hand-washing or dry cleaning, and acetate garments disintegrate when heated in atumble dryer.[63][64]The two fabrics are now required to be listed distinctly on garment labels.[65]
Cellophaneis generally made by the viscose process, but dried into sheets instead of fibers.
See also[edit]
- Cellophane– Thin, transparent sheet made of cellulose
- Hilaire de Chardonnet– French engineer, inventor of artificial silk (1839–1924)
- Nitrocellulose– Highly flammable compound
- Neuroplastic effects of pollution– Effects of pollution on the brain
- Polyester– Category of polymers, in which the monomers are joined together by ester links
- Ray P. Dinsmore– Polymer scientist
References[edit]
- ^"Viscose CV Introduction".www.swicofil.com.
- ^"WEAVING A STORY → Franklin Till".www.franklintill.com.Retrieved2022-12-02.
- ^Camille."3 Basic Types of Fabric: Synthetic Fiber, Semi-Synthetic Fiber, & Natural Fiber Defined".Retrieved2023-09-04.
- ^Kauffman, George B. (1993). "Rayon: the first semi-synthetic fiber product".Journal of Chemical Education.70(11): 887.Bibcode:1993JChEd..70..887K.doi:10.1021/ed070p887.
- ^abcdKrässig, Hans; Schurz, Josef; Steadman, Robert G.; Schliefer, Karl; Albrecht, Wilhelm; Mohring, Marc; Schlosser, Harald (2002). "Cellulose".Ullmann's Encyclopedia of Industrial Chemistry.Weinheim: Wiley-VCH.doi:10.1002/14356007.a05_375.pub2.ISBN978-3527306732.
- ^abBurchard, Walther; Habermann, Norbert; Klüfers, Peter; Seger, Bernd; Wilhelm, Ulf (1994). "Cellulose in Schweizer's Reagent: A Stable, Polymeric Metal Complex with High Chain Stiffness".Angewandte Chemie International Edition in English.33(8): 884–887.doi:10.1002/anie.199408841.
- ^abcdeNijhuis, Michelle (2009)."Bamboo Boom: Is This Material for You?".Scientific American.19(2): 60–65.Bibcode:2009SciAm..19f..60N.doi:10.1038/scientificamericanearth0609-60(inactive 2024-04-08).
{{cite journal}}
:CS1 maint: DOI inactive as of April 2024 (link) - ^abcdeSwan, Norman; Blanc, Paul (20 February 2017)."The health burden of viscose rayon".ABC Radio National.
- ^abcd"Regenerated cellulose by the Lyocell process, a brief review of the process and properties".BioResources.2018.
- ^abcdTierney, John William (2005).Kinetics of Cellulose Dissolution in N-MethylMorpholine-N-Oxide and Evaporative Processes of Similar Solutions(Thesis).
- ^abWoodings, Calvin R."A Brief History of Regenerated Cellulosic Fibres".Woodings Consulting Ltd. Archived fromthe originalon 22 April 2012.Retrieved26 May2012.
- ^Over 100 years old and still going strong From Glanzstoff (artificial silk) factory to industry park.industriepark-oberbruch.de
- ^Verinigte Glanstoff Fabrikenmerged with theNederlandse Kunstzijdefabriekenin 1929 to form theAlgemene Kunstzijde Unie,AkzoNobel's predecessor.[citation needed]
- ^abKrässig, Hans; Schurz, Josef; Steadman, Robert G.; Schliefer, Karl; Albrecht, Wilhelm; Mohring, Marc; Schlosser, Harald (2002). "Cellulose".Ullmann's Encyclopedia of Industrial Chemistry.Weinheim: Wiley-VCH.doi:10.1002/14356007.a05_375.pub2.ISBN978-3527306732.
- ^abJ. P. Bemberg AGwas one of theVereinigte Glanzstoff-Fabrikenwhich merged into the Dutch basedAlgemene Kunstzijde Unie(AKU)—AkzoNobeltoday.[citation needed]
- ^Day, Lance; Ian McNeil (1998).Biographical Dictionary of the History of Technology.Taylor & Francis. p. 113.ISBN0-415-19399-0.
- ^abWheeler, Edward (1928).The Manufacture of Artificial Silk With Special Reference to the Viscose Process.New York: D. Van Nostrand company.
- ^"Blogger".Archived fromthe originalon 2015-07-22.
- ^Varian, Brian D. (2022-08-18)."Protection and the British rayon industry during the 1920s".Business History.64(6): 1131–1148.doi:10.1080/00076791.2020.1753699.ISSN0007-6791.S2CID219025238.
- ^Varian, Brian D. (2019)."The growth of manufacturing protection in 1920s Britain".Scottish Journal of Political Economy.66(5): 703–711.doi:10.1111/sjpe.12223.ISSN0036-9292.
- ^Owen, Geoffrey (2010).The Rise and Fall of Great Companies: Courtaulds and the Reshaping of the Man-Made Fibres Industry.OUP/Pasold Research Fund.ISBN9780199592890.
- ^abcdefgJohnathan Y. Chen. Textiles and fashion: materials, design and technology, 2015. As quotedby Elsevier
- ^"Millson Award for Invention".AATCC.
- ^us 4246332,Mcorsley, C., "Process for Shaped Cellulose Article Prepared from Solution Containing Cellulose Dissolved in a Tertiary Amine N-oxide Solvent", published 1981New York, New York, Akzona Incorporated.
- ^abcdef"Lenzing Acquires TENCEL®, 2004".Archived fromthe originalon 2010-03-23.Retrieved2010-01-13.
- ^Introducing Tencel lyocell.
- ^abIpsen, Erik (25 February 1993)."INTERNATIONAL MANAGER: Freed of Textile Business, Courtaulds Is Doing Fine".International Herald Tribune.
- ^Beacham, Will."Explosion and fire halts 'Lyocell' output at Lenzing's Heiligenkreuz, Austria plant".ICIS Explore.
- ^"Bulletin EU 6-1998 (en): 1.3.50 | Akzo Nobel/Courtaulds".Europa.Archived fromthe originalon 22 September 2008.Retrieved13 November2015.
- ^abcJoyce A. Smith."Rayon – The Multi-Faceted Fiber".Ohio State University Rayon Fact Sheet.
- ^ab"Production System".www.asahi-kasei.co.jp.
- ^ab"Rayon Fiber (Viscose)".afma.org.Archived fromthe originalon April 6, 2008.
- ^abcBlanc, Paul D (2017).Fake silk: the lethal history of viscose rayon.Yale University Press.ISBN978-0-300-20466-7.OCLC961828769.
- ^abcMonosson, Emily (2016). "Toxic textiles".Science.354(6315): 977.Bibcode:2016Sci...354..977M.doi:10.1126/science.aak9834.PMID27884997.S2CID45869497.
- ^LaBat, Karen L. & Salusso, Carol J. (2003).Classifications & Analysis of Textiles: A Handbook.University of Minnesota.
- ^abcKadolph, Sara J. & Langford, Anna L. (2001).Textiles(9 ed.). Prentice Hall.ISBN978-0-13-025443-6.
- ^"Viscose vs. Modal vs. Lyocell – Difference?".Robert Owen Undershirts Co.Retrieved2018-06-11.
- ^ab"How to Wash Modal Clothes".The Spruce.Retrieved2018-06-11.
- ^"Viscose vs. Modal vs. Lyocell – Difference?".Robert Owen Undershirts Co.Retrieved2018-06-11.
- ^"What is Modal fabric? Discover the eco-friendly fabric modal".
- ^"Global Viscose Fiber Market Share, Size, Key Players Analysis, Revenue, Growth Rate and Future Outlook to 2025".Reuters.Retrieved16 July2019.[dead link]
- ^Colbond History.colbond.us. Acordis was a spinoff byAkzoNobelin 2000 after it had acquiredCourtaulds.It was throughAkzoNobel's original parent company's, theNederlandse Kunstzijdefabriek(ENKA), a joint venture withRento Hofstede Crull'sDe Vijf,namedDe Internationale Spinpot Exploitatie Maatschappij(ISEM) that the commercial production of rayon was made viable. Hofstede Crull had supplied the solution for the problem of manufacturing rayon with hisDriving Device For A Centrifugal Spinning Machinein 1925 (1931U.S. patent 1,798,312). TheISEMwas fully integrated with theAlgemene Kunstzijde Unie,the Nederlandse Kunstzijdefabriek's successor, with the death of Hofstede Crull in 1938. (SeeAkzoNobel,American Enka Company,and alsoRento Hofstede Crull.)
- ^"North American Rayon Corporation and American Bemberg Corporation"in the Tennessee Encyclopedia
- ^North American Rayon Corporation of Tennessee was an American subsidiary ofJ. P. Bemburg A.G.which was part of theVereinigte Glanstoff Fabrikenthat were absorbed into the DutchAKU,AkzoNobeltoday
- ^"Textile: Indonesia's New Export Darling".The Jakarta Globe.Retrieved16 July2019.
- ^Park, Chung Hee; Kang, Yun Kyung; Im, Seung Soon (2004)."Biodegradability of cellulose fabrics".Journal of Applied Polymer Science.94:248.doi:10.1002/app.20879.
- ^Austin, Jean; Richardson, C. H. (1941)."Ability of the firebrat to damage fabrics and paper".Journal of the New York Entomological Society.49(4): 357–365.
- ^Lindsay, Eder (1940). "The biology of the silverfish, Ctenolepisma longicaudata Esch. with particular reference to its feeding habits".Proceedings of the Royal Society of Victoria.New Series.40:35–83.
- ^Abundance of microplastics in the world's deep seas(2014-12-16). Retrieved on 2014-12-17.
- ^Comnea-Stancu, Ionela Raluca; Wieland, Karin; Ramer, Georg; Schwaighofer, Andreas; Lendl, Bernhard (20 September 2016)."On the Identification of Rayon/Viscose as a Major Fraction of Microplastics in the Marine Environment: Discrimination between Natural and Manmade Cellulosic Fibers Using Fourier Transform Infrared Spectroscopy".Applied Spectroscopy.71(5): 939–950.doi:10.1177/0003702816660725.PMC5418941.PMID27650982.
- ^Suaria, Giuseppe; Achtypi, Aikaterini; Perold, Vonica; Lee, Jasmine R.; Pierucci, Andrea; Bornman, Thomas G.; Aliani, Stefano; Ryan, Peter G. (2020-06-01)."Microfibers in oceanic surface waters: A global characterization".Science Advances.6(23): eaay8493.Bibcode:2020SciA....6.8493S.doi:10.1126/sciadv.aay8493.ISSN2375-2548.PMC7274779.PMID32548254.
- ^ab"Chapter 5.4: Carbon disulfide".Air Quality Guidelines(PDF)(2 ed.). WHO Regional Office for Europe, Copenhagen, Denmark. 2000. Archived fromthe original(PDF)on 18 October 2022.Retrieved31 July2021.
- ^abcSupreme Court of Alabama.Courtaulds Fibers, Inc. v. Horace L. Long, Jr., et al.;Horace L. Long, Jr., et al. v. Courtaulds Fibers, Inc.1971996 and 1972028. Decided: September 15, 2000.
- ^abBlanc, Paul David (2016).Fake Silk The Lethal History of Viscose Rayon.Yale University Press. p. 325.ISBN9780300204667.
- ^"Carbon Disulfide Health Effects Assessment".
- ^abBlake, Nicola J. (2004)."Carbonyl sulfide and carbon disulfide: Large-scale distributions over the western Pacific and emissions from Asia during TRACE-P".Journal of Geophysical Research.109(D15): D15S05.Bibcode:2004JGRD..10915S05B.doi:10.1029/2003JD004259.S2CID43793469.
- ^Agnès Humbert,Notre Guerre(1946), translated into English by Barbara Mellor asRésistance, Memoirs of Occupied FranceKitson's review ofRésistancein New York Sun
- ^Chou, Tzu-Chieh; Shih, Tung-Sheng; Sheu, Hamm-Min; Chang, Shu-Ju; Huang, Chin-Chang; Chang, Ho-Yuan (2004-04-25)."The effect of personal factors on the relationship between carbon disulfide exposure and urinary 2-thiothiazolidine-4-carboxylic acid levels in rayon manufacturing workers".Science of the Total Environment.322(1): 51–62.doi:10.1016/j.scitotenv.2003.08.001.ISSN0048-9697.
- ^Chou, Tzu-Chieh; Shih, Tung-Sheng; Tsai, Jui-Chen; Wu, Jyun-De; Sheu, Hamm-Min; Chang, Ho-Yuan (September 2004)."Effect of occupational exposure to rayon manufacturing chemicals on skin barrier to evaporative water loss".Journal of Occupational Health.46(5): 410–417.doi:10.1539/joh.46.410.ISSN1341-9145.PMID15492459.
- ^"5 Toxic Textiles to Avoid".Sustainable Fashion - Eco Design - Healthy Lifestyle - Luxiders Magazine.2019-12-16.Retrieved2024-04-26.
- ^Balser, Klaus; Hoppe, Lutz; Eicher, Theo; Wandel, Martin; Astheimer, Hans‐Joachim; Steinmeier, Hans; Allen, John M. (2004). "Cellulose Esters".Ullmann's Encyclopedia of Industrial Chemistry.Weinheim: Wiley-VCH.doi:10.1002/14356007.a05_419.pub2.ISBN9783527303854.
- ^Urbanski, Tadeusz (1965).Chemistry and Technology of Explosives.Vol. 1. Oxford: Pergamon Press. pp. 20–21.
- ^Centeno, Antonio (21 September 2010)."Synthetic Fabrics and Menswear – Rayon and Acetate".Real Men Real Style.Archivedfrom the original on November 5, 2012.
- ^"Fiber Characteristics: Acetate".Fabric Link.Archivedfrom the original on September 25, 2013.
- ^"Rayon and Acetate Fabrics to be Separately Labelled in Future".The Southeast Missourian.February 12, 1952.RetrievedDecember 25,2013.
Further reading[edit]
- Blanc, Paul David (2016).Fake silk: the lethal history of viscose rayon.New Haven: Yale University Press. p. 328.ISBN9780300204667.
- Gupta, VB; Kothari, VK and Sengupta, AK eds. (1997)Manufactured Fibre Technology.Chapman & Hall, London.ISBN9780412540301.
- For a review of all rayon production methods and markets see"Regenerated Cellulose Fibres"(book – Edited by C R Woodings) Hardback 2001,ISBN1-85573-459-1,Woodhead Publishing Ltd.
- For a description of the production method at a factory in Germany inWorld War II,seeAgnès Humbert(tr. Barbara Mellor)Résistance: Memoirs of Occupied France,London, Bloomsbury Publishing PLC, 2008ISBN978-0-7475-9597-7(American title:Resistance: A Frenchwoman's Journal of the War,Bloomsbury, USA, 2008) pp. 152–155
- For a complete set of photographs of the process see"The Story of Rayon" published by Courtaulds Ltd (1948)
- Arnold Hard, the textile journalist, produced two books documenting the experiences of some of the pioneers in the early British rayon industry the Hard, Arnold. H. (1933).The Romance of Rayon.Whittaker & Robinson, Manchester and Hard, Arnold (1944)The Story of Rayon,United Trade Press Ltd, London