Tesla valve

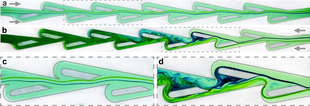
(a) Forward direction. Two adjacent filaments remain in the central corridor of the conduit with only small lateral deflections.
(b) Reverse direction. The filaments ricochet off the periodic structures, deflecting increasingly sharply before being rerouted around the 'islands' and mixing.
(c) and (d) are zoomed-in images
ATesla valve,called avalvular conduitby its inventor, is a fixed-geometry passivecheck valve.It allows afluidto flow preferentially in one direction, without moving parts. The device is named afterNikola Tesla,who was awardedU.S. patent 1,329,559in 1920 for its invention. The patent application describes the invention as follows:[1]
The interior of the conduit is provided with enlargements, recesses, projections, baffles, or buckets which, while offering virtually no resistance to the passage of the fluid in one direction, other than surface friction, constitute an almost impassable barrier to its flow in the opposite direction.
Tesla illustrated this with the drawing, showing one possible construction with a series of eleven flow-control segments, although any other number of such segments could be used as desired to increase or decrease the flow regulation effect.
Diodicity
[edit]The valves are structures that have a higher pressure drop for the flow in one direction (reverse) than the other (forward). This difference in flow resistance causes a net directional flow rate in the forward direction in oscillating flows. The efficiency is often expressed in diodicity,being the ratio of directional resistances.
The flow resistance is defined, analogously toOhm's lawfor electrical resistance,[2]as the ratio of applied pressure drop and resulted flow rate:
whereis the applied pressure difference between two ends of the conduit, andthe flow rate.
The diodicity is then the ratio of the reversed flow resistance to the forward flow resistance: .If,the conduit in question has diodic behavior.
Thus diodicity is also the ratio of pressure drops for identical flow rates:[3]
whereis the reverse flow pressure drop, andthe forward flow pressure drop for flow rate.
Equivalently, diodicity could also be defined as ratio of dimensionlessHagen numberorDarcy friction factorat the same Reynolds number.[4]
Applications
[edit]With no moving parts, Tesla valves are much more resistant to wear and fatigue, especially in applications with frequent pressure reversal such as apulsejet.[5]

The Tesla valve is used inmicrofluidicapplications[7]and offers advantages such as scalability, durability, and ease of fabrication in a variety of materials.[8]It is also used in macrofluidic applications and pulse jet engines.[4]In 2021 Xiaomi announced that some of their mobilephones will be using Loop liquid cooling technology. This technology uses a Tesla valve to make sure that the coolant flow is unidirectional.[9][10]

The upper figure shows flow in the blocking direction: at each segment, part of the fluid is turned around (red) and interferes with the forward flow (black).
The lower figure shows flow in the unimpeded direction (blue).
Onecomputational fluid dynamicssimulation of Tesla valves with two and four segments showed that the flow resistance in the blocking (or reverse) direction was about 15 and 40 times greater, respectively, than the unimpeded (or forward) direction.[11]This lends support to Tesla's patent assertion that in the valvular conduit in his diagram, a pressure ratio "approximating 200 can be obtained so that the device acts as a slightly leaking valve".[1]
Steady flow experiments, including with the original design, however, show smaller ratios of the two resistances in the range of 2 to 4.[4]It has also been shown that the device works better with pulsatile flows.[4]
See also
[edit]References
[edit]- ^ab"Patent #: US001329559".United States Patent and Trademark Office.Office of the Chief Communications Officer.Archivedfrom the original on 3 January 2017.Retrieved2 January2017.
- ^Nguyen, Quynh M.; Huang, Dean; Dean, Evan; Romanelli, Genievieve; Meyer, Charlotte; Ristroph, Leif (Oct 2020). "Tesla's fluidic diode and the electronic-hydraulic analogy".American Journal of Physics.89(4): 393–402.arXiv:2103.14813.doi:10.1119/10.0003395.S2CID232401497.
- ^de Vries; Florea; Homburg; Frijns (2017)."Design and operation of a tesla-type valve for pulsating heat pipes".International Journal of Heat and Mass Transfer.105:1–11.doi:10.1016/j.ijheatmasstransfer.2016.09.062.
- ^abcdNguyen, Quynh M.; Abouezzi, Joanna; Ristroph, Leif (17 May 2021)."Early turbulence and pulsatile flows enhance diodicity of Tesla's macrofluidic valve".Nature Communications.12(12): 2884.arXiv:2103.17222.Bibcode:2021NatCo..12.2884N.doi:10.1038/s41467-021-23009-y.PMC8128925.PMID34001882.
- ^Mohammadzadeh, K.; Kolahdouz, Ebrahim M.; Shirani, E.; Shafii, M. B. (2013)."Numerical study on the performance of Tesla type microvalve in a valveless micropump in the range of low frequencies".Journal of Micro-Bio Robotics.8(3–4): 145–159.doi:10.1007/s12213-013-0069-1.S2CID109638783.Archivedfrom the original on 2021-04-23.Retrieved2021-05-12.
- ^Forster, Fred K.; Bardell, Ronald L.; Afromowitz, Martin A.; Sharma, Nigel R. (1995).Design, fabrication and testing of fixed-valve micro-pumps.Proceedings of the ASME Fluids Engineering Division.Vol. 234. pp. 39–44.
- ^Deng, Yongbo; Liu, Zhenyu; Zhang, Ping (28 Jan 2010)."Optimization of no-moving part fluidic resistance microvalves with low reynolds number".2010 IEEE 23rd International Conference on Micro Electro Mechanical Systems (MEMS).pp. 67–70.doi:10.1109/MEMSYS.2010.5442565.ISBN978-1-4244-5761-8.S2CID22740698.Archivedfrom the original on 12 May 2021.Retrieved12 May2021.
- ^Gamboa, Adrian R.; Morris, Christopher J.; Forster, Fred K. (2005). "Improvements in Fixed-Valve Micropump Performance Through Shape Optimization of Valves".Journal of Fluids Engineering.127(2): 339.doi:10.1115/1.1891151.S2CID55961879.
- ^"Explained: How liquid cooling technology works in smartphone".
- ^"Liquid cooling and Tesla valves are coming to smartphones".
- ^"Tesla's Valvular Conduit - Fluid Power Journal".Fluid Power Journal.2013-10-23. Archived fromthe originalon 2017-01-13.Retrieved2017-01-13.